Ceramic Electrodes and Electrolytes
The Braun Group researches on renewable energy sources for a safe, clean environment and a sustainable energy economy. Focus is the discovery and elucidation of principal mechanisms, which control behavior and properties of ceramics, in particular the correlation between materials structure and transport properties for electrochemical storage and conversion systems, the interaction of surfaces with gases, liquids, light, and organic matter.
For the understanding of structure-property relationships on the mesoscopic and molecular scale, we develop and employ operando and in situ synchrotron x-ray and neutron scattering and spectroscopy methods, along with electrochemical and electroanalytical techniques. We collaborate with high profile partners worldwide.
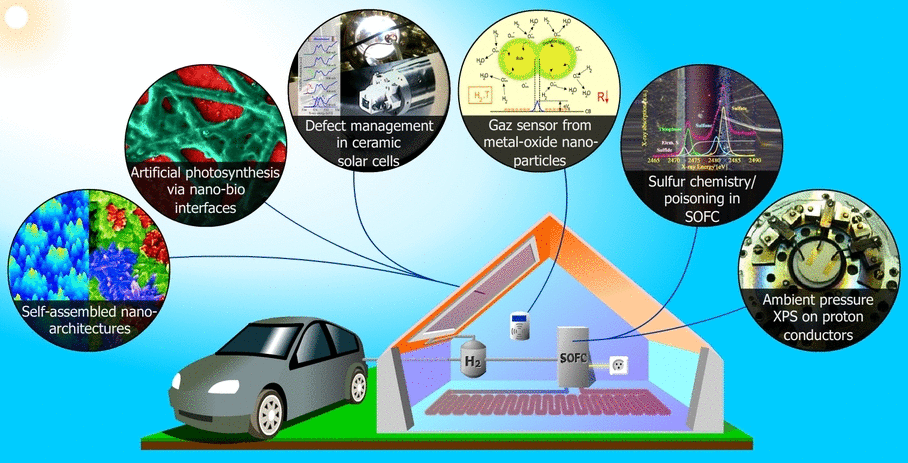
Our Research Topics
- Photoelectrochemical cells (PEC) for solar hydrogen, ammonia and CO2 reduction
- Photonic light trapping for photoelectrochemical water splitting
- Semiconductor photoelectrochemistry
- Neutron and X-ray methods for analysis of solid oxide fuel cells, batteries, and solar cells
- Nano-bio hybrid structures for artificial photosynthesis
- Development of neutron and X-ray operando in situ electrochemical methods
- Self organization and pattern formation for photoelectrode design
- Operando, in situ electrochemical and ex situ synchrotron studies on lithium ion batteries
- Gas sensors from metal oxide nano-particles
- Charge transport and charge carrier dynamics
- Human capacity building in Africa
News July 2025: New paper accepted: "Resilience of Hybrid Bioelectrodes in an Ionizing Environment: A Space Simulation Study of Limnospira indica Under Gamma Radiation", to appear in "Astrobiology"; DOI: 10.1177/15311074251365212 .
News March 2025: Media coverage by SRF1 Wissenschaftmagazin (18'50'' - 20'50'') of our campaign on cyanobacteria at Jungfraujoch.
News March 2025: I am happy MRS accepts me as one of their MRS Fellows in 2025.
News March 2025: We welcome Physics Professor Dr. Selma Erat from Mersin University for her SNF Research Visit.
News January 2025: We welcome our project collaborators Prof. Joey Ocon and Dr. DJ Matienzo from U Philippines Diliman for their project visit.
News January 2025: New paper accepted with Qianli Chen group and colleagues from Korea, USA, France on ambient pressure XPS on proton conductors.
News December 2024: We congratulate PhD student Kidan G. Gebremariam for her L'Oreal UNESCO 2024 Award.
News September 2024: We welcome Ethiopian Physicist and ESKAS Fellow PhD student Kidan G. Gebremariam in our group.
News August 2024: New paper published - Restructurable materials for soft actuators, Qing Chen, Invited Feature Paper—Review MRS Distinguished Invited Speaker, Journal of Materials Research (2024). https://doi.org/10.1557/s43578-024-01423-4
News August 2024: New paper published - Fluorescence and electron transfer of Limnospira indica functionalized biophotoelectrodes, Ryzhkov, Nikolay; Colson, Nora; Ahmed, Essra; Pobedinskas, Paulius; Haenen, Ken; Janssen, Paul; Braun, Artur, Photosynthesis Research, https://doi.org/10.1007/s11120-024-01114-5
News July 2'024: 2nd edition of Artur Braun's book published. X-Ray Studies on Electrochemical Systems - Synchrotron Methods for Energy Materials, Artur Braun In der Reihe De Gruyter Textbook https://doi.org/10.1515/9783110794038
News July 2024: New paper published - Electric Polarization-Dependent Absorption and Photocurrent Generation in Limnospira indica Immobilized on Boron-Doped Diamond, Ryzhkov, Nikolay, Colson, Nora, Ahmed, Essraa, Pobedinskas, Paulius, Haenen, Ken. Braun, Artur, Janssen, Paul J., ACS Omega https://doi.org/10.1021/acsomega.4c03925
News May 2024: New paper published - Hygro-Dynamic and Conductive Actuator That Restructures and Heals by Water; Qing Chen, Tina Künniger, Qun Song, Kai Zhang, Andrei Chumakov, Yusuf Bulut, Constantin Harder, Peter Müller-Buschbaum, Stephan V. Roth, Artur Braun; First published: 23 May 2024 https://doi.org/10.1002/adfm.202402924
News May 2024: PhD student Mrs. Gebremariam Kidan Gebreegziabher from Addis Ababa University, Ethiopia, has been selected as main applicant for the Swiss Government Excellence Scholarship 2023-2024, and will be researching for one year in Braun's group at Empa from 1 September 2024 - 31 August 2025.
News April 2024: Braun, and Profs. Danielle Mai from Stanford University, Minkyu Kim from University of Arizona, Newaye Tegegne from Addis Ababa University, organize the Symposium "Bio-based and Biomimetic Polymers in Soft Robotics" at the MRS Spring Meeting 2024 in Seattle, WA, United States. Meeting Chairs Mmantsae Diale and Martin Kaltenbrunner are among the invited speakers. Among the MRS Best Poster Award Winners was also a poster from our Symposium: Yongyi Zhao, SB11.07.07 "A Self-Healing ElectricallyConductive OrganogelComposite". This Symposium is inspired by the COgITOR project.
News 11 February 2024: We welcome "returning" Visiting Professor Joey D. Ocon from University of the Phillipines Diliman, who spends his second stay at Empa now.
News 11 February 2024: We welcome Professor Julie Anne Del Rosario Paraggua from University of the Philippines Diliman, who will stay for one week and deliver a seminar talk with title "Levelized cost of hydrogen produced via solar- and wind-powered electrolysis in the Philippines".
News 01 February 2024: We welcome PhD student Ms. Glennise Faye Mejica from University of the Phillipines Diliman, who will be researching for two months on photoelectrochemical ammonia synthesis finded by the Swiss ASEAN project "Aurora".
News 23 November 2023: Dr. Nikolay Ryzhkov visits University of the Philippines Diliman and presents "Bio- and biomimicking interfaces for smart materials design and alternative energy harvesting".
News 07 October 2023: Artur Braun experiences rocket attacks during his sabbatical at Weizmann Institute of Science, Rehovot, Israel.
News 28 September 2023: Manuscript accepted by Advanced Science (Wiley IF 17): "Entropy and Isokinetic Temperature in Fast Ion Transport", by Du, Peng; Zhu, Hong; Braun, Artur; Yelon, Arthur; Chen, Qianli.
News 30 August 2023: We congratulate our ESKAS Fellow Dr. Kwanele Kunene for her new position at Chalmers University in Sweden.
News 18 July 2023: NCSU Professor Michael F. Dickey visits our lab and delivers a seminar presentation to staff and students. Sponsored by EU COgITOR project.
News 9-13 July 2023: Prof. Joey Ocon and Dr. Donn Matienzo visit our lab and deliver seminar presentation. Sponsored by ASEAN Aurora project.
News 23 May 2023: ASU Battery Professor Candace Chan visits our lab and delivers a seminar presentation to staff and students. Sponsored by EU OpMetBat project.
Projects & Funding Agencies
Project Akronym | Description | Logo | Period |
---|---|---|---|
HYMETBAT | Hybrid metrology for sustainable and low-carbon footprint battery materials | 2025-2028 | |
SHINE |
Solar Harvesting and Integration to Photoelectrochemical Cell for Nitrogen Economy; with Univ. of the Philippines Diliman, Prof. Joey Ocon |
2024-2025 | |
3DCyan |
3D Printed Algal Biophotoelectrochemical Reactor For PV And Solar Fuel Production |
Korean-Swiss Science and Technology Programme (KSSTP)
|
2023-2026 |
Aurora | Renewable Ammonia with Univ. of the Philippines Diliman, Prof. Joey Ocon | 2023 | |
OpMetBat |
Operando metrology for energy storage materials |
2022 - 2025 | |
HySPARC | Sustainable hydrogen production in space by radiation hard cyanobacterial biofilms in a photoelectrochemical (PEC) system using boron-doped diamond (BDD) electrodes | ![]() |
2022 - 2025 |
COgITOR |
A new colloidal cybernetic system towards 2030 |
|
2021 - 2025 |
ESKAS | Electrosynthesis of Ammonia (South Africa) | 2022 - 2023 | |
PROTONIQUE 3 |
Proton conductivity in epitaxial strained thin films |
2021 - 2025 | |
PHOGAM |
Flanders/Swiss Lead Agency Process: Charge and energy transfer between cyanobacteria and semiconductor electrodes under gamma-irradiation |
|
|
SUNRISE | Solar Energy for a Circular Economy | ||
Yonsei | Electrochemistry of the thylakoid membrane - metal oxide electrode assemblies | ||
GIST |
SNF Korean Swiss project: Molecular and physical aspects of dye sensitization of photoelec-trodes with copper-based sensitizer molecules |
||
SSAJRP | Production of Liquid Solar Fuels from CO2 and Water: Using Renewable Energy Resources | ||
Pattern Formation for PEC | Reaction-diffusion processes for the growth of patterned structures and architectures: A bottom-up approach for photoelectrochemical electrodes | ||
PEC EPFL | Defects in the bulk and on surfaces and interfaces of metal oxides with photoelectrochemical properties: In-situ photoelectrochemical and resonant x-ray and electron spectroscopy studies | ||
NANOPEC | Nanostructured Photoelectrodes for Energy Conversion | ![]() |
|
SOFC-Life | Solid Oxide Fuel Cells – Integrating Degradation Effects into Lifetime Prediction Models | ![]() |
|
MetInsTra | X-ray and electrochemical studies on solid Oxide fuel cells and related materials | ||
HITEMPECHEM | X-ray and electrochemical studies on solid Oxide fuel cells and related materials | ![]() |
Organized Conferences, Symposia & Workshops
Year | Role | Event | Participants | Location |
---|---|---|---|---|
2025 | Co-Organizer Artur Braun, with Elena Rozhkova, Qianli Chen, WonHyoung Ryu | MRS Spring Meeting Symposium on "Protons in Solids, Fluids, and Molecules" | Seattle, USA | |
2024 | Co-Organizer Artur Braun, with Minkyu Kim, Danielle J. Mai, Newayemedhin Aberra Tegegne | MRS Spring Meeting Symposium on bio inspired soft robotics | 300 | Seattle, USA |
2023 | Area Coordinator Artur Braun, with Gesa Beck | EUROMAT H: Materials for Circularity and Sustainability | 1000 | Frankfurt, Germany |
2021 | Co-Organizer Artur Braun, with Nicolas Gaillard, Elena Rozhkova | PACIFICHEM, Hawai'i / Symp. Artificial Photosynthesis | 150 | Honolulu, Hawai'i, USA |
2019 | Lead-Organizer Artur Braun, Rita Toth | SUNRISE Flagship Stakeholder Workshop | 30 | Empa, Switzerland |
2017 | Co-Organizer Rita Toth, with Mmantsae Diale, | MRS Fall Meeting Symposium | Boston MA, USA | |
2017 | Co-Organizer Artur Braun | ALS User Meeting Workshop: Synchrotron Bio Materials | 30 | Berkeley CA, USA |
2015 | Co-Chair Artur Braun, with Hongyou Fan, Ken Haenen, Lia Stanciu, Jeremy A. Theil | MRS Spring Meeting 2015 | 5'500 | San Francisco CA, USA |
2015 | Lead Artur Braun | Int'l Expl. Workshop PEC, Cat. & X-ray | 30 | Empa, Switzerland |
2013 | Lead Artur Braun | Int'l Expl. Workshop X-ray Electrochemistry | 30 | Empa, Switzerland |
2013 | Co-Organizer Artur Braun, with Arndt Remhof, | ESS Science Symposium: Future Energy | 40 | PSI/SINQ, Switzerland |
2013 | Co-Organizer Artur Braun, with Elena Rozhkova | MRS Spring Meeting Symposium Artificial Photosynthesis | 100 | San Francisco CA; USA |
2012 | Co-Organizer Artur Braun | MRS Fall Meeting; Symposium Frontier Chemical Imaging | 100 | Boston MA, USA |
2012 | Co-Organizer Artur Braun | MSE Symposium D4 “Thin Films”, Darmstadt | 40 | Darmstadt, Germany |
2011 | Lead Organizer Artur Braun | MRS Spring Symposium on Protons in Solids | 80 | San Francisco CA, USA |
2011 | Co-Organizer Artur Braun | E-MRS Spring Meeting Symposium, Materials for solar hydrogen | 80 | Nice, France |
2010 | Lead Organizer Artur Braun | MRS Spring Symp Energy Materials Synchrotron Neutron | 100 | San Francisco CA, USA |
2010 | Lead Organizer Artur Braun, with Clemens Heske, Matthew Marcus, Jingha Guo | Advanced Light Source Users Meeting Workshop | 25 | Berkeley CA, USA |
2009 | Lead Organizer ArturBraun, with P. Alivisatos , Egbert Figgemeier , John Turner , Jinhua Ye | MRS Spring Meeting Symposium Photoelectrochemistry | 250 | San Francisco CA, USA |
2009 | Lead Organizer Artur Braun,with Clemens Heske, Jinghua Guo, Hendrik Bluhm | ALS Users Meeting Workshop Soft X-Ray Renewable Energy | 25 | Berkeley CA, USA |
2008 | Co-Organizer Selma Erat | Empa PhD Symposium | St. Gallen, Switzerland | |
2006 | Assistant of Organizer, with Peter Holtappels | MODVAL3 Workshop Modelling & Validation Fuel Cells | 40 | Empa, Switzerland |
Presentations by Group Members, Visitors & Guests
Name | Affiliation | Title | Conference | Place | Date |
---|---|---|---|---|---|
MSc Kidan Gebremariam | Empa, ETHZ and Addis Ababa University |
Charge carrier dynamics at the electron transport layer/organic interface in organic solar cells |
ESKAS Project | Empa, Dübendorf | 22 July 2025 |
Dr. Paul J. Janssen | SCK CEN, Mol, Belgium | Sustainable, functional material on biobasis | PHOGAM Project | Empa, Dübendorf | 5 June 2024 |
Dr. Qing Chen | Braun Group | The Design, Fabrication and Structural Modeling of Biomimetic Soft Materials for Robotic Applications | MRS Spring Meeting; COgITOR; Distinguished Invited Speaker | Seattle, WA, United States | 23 April 2024 |
Dr. Qing Chen | Braun Group | A hierarchical fabriaction strategy for multi-responsive actuators and with structural reconfiguration-assisted self-healing avbility | DPG Tagung Berlin, invited talk (Hauptvortrag) | Berlin | 22 March 2024 |
Assoc.-Prof. Julie Anne Paraggua | UP Diliman, Philippines |
Levelized cost of hydrogen produced via solar- and wind-powered electrolysis in the Philippines |
Empa Seminar | Empa, Dübendorf | 13 February 2024 |
Dr. Nikolay Ryzhkov | Braun Group |
Bio- and biomimicking interfaces for smart materials design and alternative energy harvesting |
DChE Seminar | UP Diliman, Philippines | 23 November 2023 |
MSc Nora Colson | Hasselt Univ., Braun Group | Welcome Presentation | Internal: ESA HySPARK Project | Empa Dübendorf | 1 September 2023 |
Dr. Kwanele Kunene | Braun Group | Farewell Presentation of ESKAS Fellow | Internal: ESKAS Project | Empa Dübendorf | 30 August 2023 |
Dr. Loghman Jamilpanah | Braun Group, Hug Group |
Developing Metallic Multilayers Hosting Different Skyrmion Types Toward Local Control via Electric Fields (Poster) |
13th Joint European Magnetic Symposia | Madrid, Spain | 29 August 2023 |
Dr. Nikolay Ryzhkov | Braun Group |
Electric polarization effect on photosynthetic efficiency, non-photochemical quenching and photovoltaic performance of intact Limnospira indica based photoelectrodes |
20th Congress of the European Society for Photobiology |
Lyon, France |
28 August 2023 |
Dr. Qing Chen | Braun Group |
Multi-sensing and self-healing skin for robotic applications |
ACS Fall Meeting 2023 | San Francisco, California | 16 August 2023 |
Prof. Michael Dickey | North Carolina State University | Shaping a soft future | COgITOR project seminar | Empa Dübendorf | 19 July 2023 |
Prof. Joey Ocon & Dr. DJ Donn Matienyo | University of The Philippines Diliman |
A Vertically Integrated Research Approach on Catalysis, Electrochemistry, and Energy Engineering |
Seminar of the ASEAN Aurora Ammonia Electrosynthesis project | Empa Dübendorf | 12 July 2023 |
Prof. Candace Chan | Arizona State University |
Nanostructured Li7La3Zr2O12 Garnet Solid-State Electrolytes: Effect of Synthesis Route on Microstructure, Ionic Conductivity, and Lithium Stripping/Plating Behavior |
OpMetBat project semina | Dübendorf, Empa | 24 May 2023 |
Dr. Artur Braun | Empa |
Parameterization of Proton Transport in Ceramic Electrolyte Membranes by Elastic Strain |
Colloquim 636 of the European Mechanical Society |
Besancon, France | 23 May 2023 |
Dr. Qing Chen | Braun Group |
Investigation of strain-induced deformation of polymer thin films with small-angle X-ray scattering (SAXS) as a tool for microstructural study |
Colloquim 636 of the European Mechanical Society
|
Besancon, France | 22 May 2023 |
Dr. Nikolay Ryzhkov | Braun Group |
Electric Polarization Effect on Photosynthetic Performance of Limnospira Immobilized at Diamond-like Carbon Electrodes |
35th Topical Meeting of the International Society of Electrochemistry |
Gold Coast, Australia | 9 May 2023 |
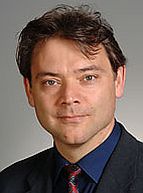
Scientists:
Dr. Alexey Rulev
Dr. Nikolay Ryzhkov
ESKAS Fellow / PhD Student
M.Sc. Physicist Kidan G. Gebremariam
Name | Position in Group | Current Position |
Selma Erat | Visiting Professor | Professor, Mersin University |
Loghman Jamilpanah | Postdoc Scientist | |
Nora Colson | Visiti9ng PhD Student | PhD Student, Hasselt Univ. |
Glennise Faye Mejica | Visiting PhD Student | PhD Student, Univ. of the Philippines |
Qing Chen | Scientist | Associate Professor, China Spallation Neutron Source |
Yang Luo | Visiting Scientist | Professor, CU Hong Kong |
Selma Erat | PhD Student ETHZ | Professor, Mersin University |
Renata Solarska | Postdoc, Swiss BfE | Professor, Warsaw University |
Debajeet K. Bora | PhD Student Uni Basel | Professor, Ben Guerir University, Morocco |
Qianli Chen | PhD Student ETHZ | Professor, Shanghai Jiao Tong University, China |
Ramin Matloub Aghdam |
MSc Student KTH | PhD EPFL, Entrepreneur, PIEMACS Sarl, Lausanne |
Kwanele Kunene | ESKAS Postdoc Fellow | Chalmers University, Sweden |
Jean-Claude Tinguely | MSc Student FH Vorarlberg | PhD, Researcher at Tromso, University of the Arctic, Norway, |
Jean-Pierre Pierog | MSc Student Univ. de Montpellier | ALSTOM, Engineer |
Romy Löhnert | BSc Student Ernst Abbe hochschule Jena | PhD, Ernst Abbe Hochschule Jena |
Dorota Flak | PhD Student AGH | Staff Scientist, Poznan University |
Simon Tymen | MSc Student Univ. de Pau | PhD Berlin, Univ. de Nantes |
Mateusz Schabikowski | MSc Student AGH | Adjunct, Polish Acad. of Sciences |
Min-Kyu Son | Postdoc | Senior Researcher, KICET, Korea |
Nikolett Nagy | BSc Student, Univ. of Szeged | MSc Univ. of Szeged |
Krzysztof Szastak | MSc Student, AGH Krakow | Project Manager |
Mahabubur Chowdhoury | Visiting Scientist, CPUT, Cape Town | Professor, CPUT, South Africa |
Edvinas Navickas | PhD Student TU Wien | Infineon Technologies |
Yelin Hu | PhD Student EPFL | BASF |
Florent Boudoire | PhD Student Uni Basel | R&D Engineer CSEM, Neuchatel |
Itani Madiba | PhD Student UNISA | Senior Researcher, Univ. of South Africa, Pretoria |
Gareth-John Moore | MSc Student U Pretoria | PhD Uni Berne, RP Photonics AG |
Kelebogile D. Mmabong | PhD Student U Pretoria | Senior Lecturer, Univ. of Botswana |
Niels Burzan | MSc Student Uni Basel | PhD, CEO Mentix Schweiz GmbH |
Gunnar Nurk | Scientist | Professor, Tartu University |
Michel Prestat | Scientist | Senior Researcher, French Corrosion Institute |
George Tsekouras | Postdoc | Research Fellow, Australian National University |
Jianjun Wang | Postdoc | Professor, Shandong University |
Tzu-Wen Huang | Postdoc | Sensor Industry, Switzerland |
Alejandro Ovalle | Postdoc | Teaching |
Rita Toth | Scientist | Coaching & Counseling |
Songhak Yoon | Scientist | Staff Scientist, Fraunhofer IWKS |
Krisztina Schrantz | Scientist, Asst.-Professor | Head EHSS, SOLVO Biotech |
Santhi Ani Joseph | Professor | St. Teresa College, Ernakulam, Kerala, India |
We were delighted to have eminent scientists visiting our group:
U Philippines Diliman |
9 January 2025 |
|
SCK CEN - Belgian Nuclear Research Centre |
4 June 2024 |
|
North Carolina State University |
18 July 2023 |
|
Arizona State University |
24 May 2023 |
|
UCSF, San Francisco |
13 March 2019 |
|
Xi'an University |
20 August 2015 |
|
iThemba LABS |
|
|
Technion |
1 September 2015 |
|
Univ. of New South Wales |
|
|
Univ. of Tokyo |
|
|
University of Pretoria |
17-19 August 2015 |
|
KAIST, Korea |
17-19 August 2015 |
|
University of Bern |
17-19 August 2015 |
|
University of Pretoria |
17-19 August 2015 |
|
GIST, Korea |
17-19 August 2015 |
|
Universität Erlangen-Nürnberg |
17-19 August 2015 |
|
Stockholm University |
17-19 August 2015 |
|
University of Graz |
17-19 August 2015 |
|
Stanford University |
17-19 August 2015 |
|
SIMIT, Shanghai |
17-19 August 2015 |
|
Xi’an Jiaotong University |
17-19 August 2015 |
|
University of Tokyo |
17-19 August 2015 |
|
CPUT, Cape Town |
17-19 August 2015 |
|
Helmholtz Zentrum Berlin |
3-5 June 2013 |
|
Helmholtz Zentrum Berlin |
3-5 June 2013 |
|
PSI SLS and ETHZ |
3-5 June 2013 |
|
PSI SLS |
3-5 June 2013 |
|
TU Berlin and DESY FEL |
3-5 June 2013 |
|
Indian Institute of Science |
3-5 June 2013 |
|
SPECS GmbH, Berlin |
3-5 June 2013 |
|
EPFL |
3-5 June 2013 |
|
HZB Berlin |
3-5 June 2013 |
|
Gwangju Institute of Technology |
3-5 June 2013 |
|
SLS |
3-5 June 2013 |
|
Canadian Light Source |
3-5 June 2013 |
|
AGH Krakow |
3-5 June 2013 |
|
SLAC SSRL |
3-5 June 2013 |
|
PSI |
3-5 June 2013 |
|
McMaster University |
3-5 June 2013 |
|
LBNL Molecular Foundry |
3-5 June 2013 |
|
Dr. Matthew Brown |
ETHZ |
3-5 June 2013 |
LBNL ALS |
3-5 June 2013 |
|
NIMS |
2008 |
|
|
|
|
Laboratory for High Performance Ceramics
Head of Laboratory Dr. Jakob Schwiedrzik |
||||||||
---|---|---|---|---|---|---|---|---|
Assistance and Support Georgiana Schönberg |
||||||||
Ceramic based composites Dr. Gurdial Blugan |
Smart ceramic processing Dr. Frank Clemens |
Nanopowders and ceramics Dr. Michael Stuer |
Ceramic electrodes and electrolytes Dr. Artur Braun |
Architectured Materials Dr. Jakob Schwiedrzik |
||||
Scientists: Dr. Camila P. Canales Dipesh K. Dubey |
Scientists: Dr. Arun Ichangi Christopher Bascucci |
Scientists: Dr. Marc Brunet-Cabre PhD Students: Annalena Erlacher
|
Scientists: Dr. Alexey Rulev
|
Scientists: Dr. Kevin Both Martina Birocco
|
Nanopowders and ceramics
Within the scope to use materials and energy ressources in the most sustainable manner, attention is put on advanced morphological, chemical and crystallographic characteristics of ceramic powders, materials and composites. Special focus is put on the multidimensional space, beyond density and grain size, and the resulting effects on the materials properties with the aim to tend towards advanced microstructure and grain boundary engineering.
Powder synthesis
Among our competences is the synthesis of functional oxide nanoparticles (by flame processes), their characterisation and processing.
Powders can be used as fillers in polymer composites and coatings, or serve as a starting material for advanced ceramic components. Hereby special focus is put on the particles characteristics such as their shape, size and phase with the purpose to enable the development of materials with new or improved properties. Engineered quality powders are key to achieve innovation with the best performance and added-value of the materials.
We perform R&D collaborations in the frame of national and international projects with partners from industry and university.
Three-dimensional shaping of ceramics
Driven by the remaining challenges in the additive manufacturing field, light-based ceramic shaping is another competence area. Studying the whole process chain, special focus is put into into powder feedstock preparation and slurry formulation. Our goals are not only to shape ceramic parts - and the future - but do so expanding and optimizing their properties.
Current research example:
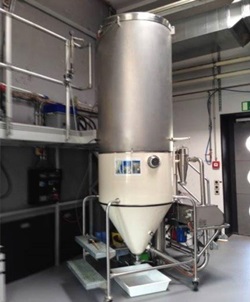
Shaping of complex shaped, high precision and reliable parts as well as the long processing time and cost-intensive post processing is a key challenge in ceramics processing. Selective laser melting could be a solution of these problems. Although it is already a well-controlled and extensively used technology in the field of metals, alloys and polymers, key problems still have to be resolved for its use on brittle materials, and especially high performance ceramics.
The inability to closely monitor and fine tune the interaction of laser light sources with ceramic based powders remains a problem. Combined with the slow sintering kinetics of ceramics, a whole research field is left to explore. This highlights the current absence of industrial SLS processes to consolidate ceramic powders into dense structures with controlled material properties.
In our research, nanosized ceramic powders are granulated by spray drying to improve the powder handling especially from a flowability and safety point of view. Focus is put on maximizing the powder bed packing density and its influence on the solid and liquid phase sintering. Furthermore, the influence of the composition and morphology of these composite granules on the light absorption is studied, which in addition to minimizing thermal stresses and cracks is a key challenge for the future.
Ceramic based filters and membranes
Filters and membranes play an increasingly important role for technological breakthroughs bringing environmental, societal and economic value. Among other materials, ceramic based ones are in this field important because of their specific properties such as heat or chemical resistance. Hereby we focus in particular on the advanced microstructural control via powder selection and processing as well as advanced doping and sintering strategies.
Current research example: Virus Filtration applying surface modified ceramics and carbon nanotubes
Water purification is necessary to prevent the spread of different diseases, caused by water-borne germs like bacteria, protozoa, and viruses. The germs may be separated from the water by a physical process, where the contaminated water is passing a porous medium like a filter or by adsorption driven separation processes. Our projects are focused on the adsorption based separation of viruses from water applying nanostructured, ceramic based filters as well as modified nanofibers originating from carbon nanotubes CNT and graphene. The biggest challenge results from the required filtering scale, namely the size of the viruses 20-50 times smaller than bacteria.
Recently we could evaluate the application of surface modified ceramic water filters for virus removal. Virus separation efficiencies (MS 2 bacteriophages and PhiX 174 bacteriophages ; size 25 nm, PZC 2 and 7 respectively) of 99 % to 99.99 % could be achieved. Such efficiencies being limited to narrow pH conditions more research is necessary to improve the systems to be compatible with common water sources. Modification of the highly active, porous ceramic surface was achieved by incorporation of nanosized inorganic particles.
As an alternative and promising solution for a broad pH spectrum, we apply CNT based fibers, after modification of the nanostructured surface.
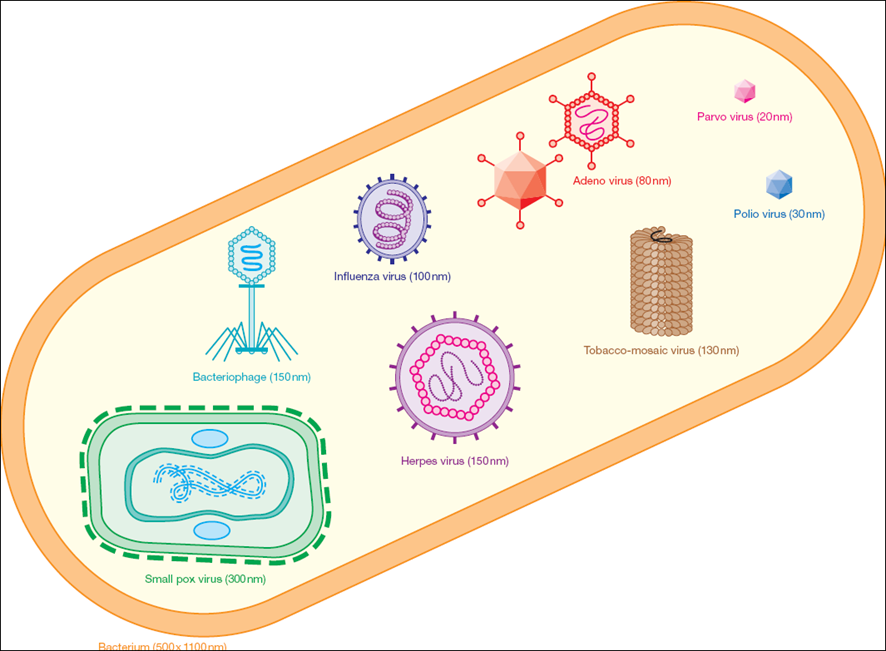
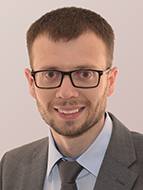
Smart ceramic processing
The focal point of the tasks lies in the interdisciplinary collaboration in the production of functional materials and composites. Developing prototypes of fibres, hollow fibers, foils and tubes is the main focus in the process development for developing novel system components.
> An overview of Smart Processing for Ceramics and Sensor-Composite Materials you find here:
Overview-PDF (982KB)
Thermoplastic forming Ceramics
The Laboratory for High Performance Ceramics is engaged in the development of thermoplastic forming and the development of thermoplastic binder systems for pressing, extrusion, injection molding, dip coating and 3D printing of ceramic components. Due to its many years of experience, the group does not focus on a specific binder system, but rather develops and optimizes customer-oriented, individual solutions. In the course of these developments, binder systems for the thermoplastic 3D printing of ceramic powders are also being developed. The additive manufacturing process of thermoplastic composites (Fused Deposition Modeling - FDM or Fused Filament Fabrication - FFF) is a recognized and widespread technology for the production of complex macroscopic structures. Empa develops thermoplastic binder systems, which enable cost-effective printing of ceramic components with conventional (open-source) FDM printers. Figure 1 shows the most important factors that influence the 3D printing of ceramics.
Figure 1: Typical factors influencing thermoplastic 3D printing of ceramic materials
blue = machine factors,
red = material failures
The 3D printing of thermoplastic ceramics offers the possibility to produce components individually via layered deposition. Typically, thermoplastic filaments are fed into a heated nozzle via a Bowden extruder. The polymer binder is melted and deposited in a desired position. After cooling and hardening, a structure with a layer thickness between 0.03 and 1.2 mm can built up.
The process is divided into several production steps:
- Compounding of the ceramic powder and the thermoplastic binder
- Filament or granule production for thermoplastic 3D printing
- 3D printing by melting the filament and layered deposition of the material
- Thermal treatment (debinding and sintering of the components)
Post-treatment of the component surface can be done on the printed, debinded or sintered state. Figure 2 shows a commercially available simple 3D printer used for materials development.
Figure 2: Commercially available 3D printer for the development of thermoplastic ceramic materials.
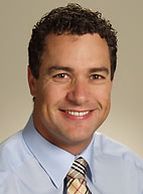
Scientists:
Dr. Arun Ichangi
Dr. Elham Montakhab
PhD-Students:
Christopher Bascucci
Sofiia Butenko
visiting PhD-Student:
Ceramic-based Composites
We design, process and characterize ceramic based composites for innovative and challenging structural and functional applications. Projects are the center of attention, in which
- ceramic-ceramic composites (CMC),
- micro and macro layered structures (laminates),
- polymer derived ceramic composites (PDC),
- coatings,
- graded materials (FGM) and
- ceramics joined to metals
are required. We develop new and optimize state of the art production routes and transfer know-how and technologies to industry.
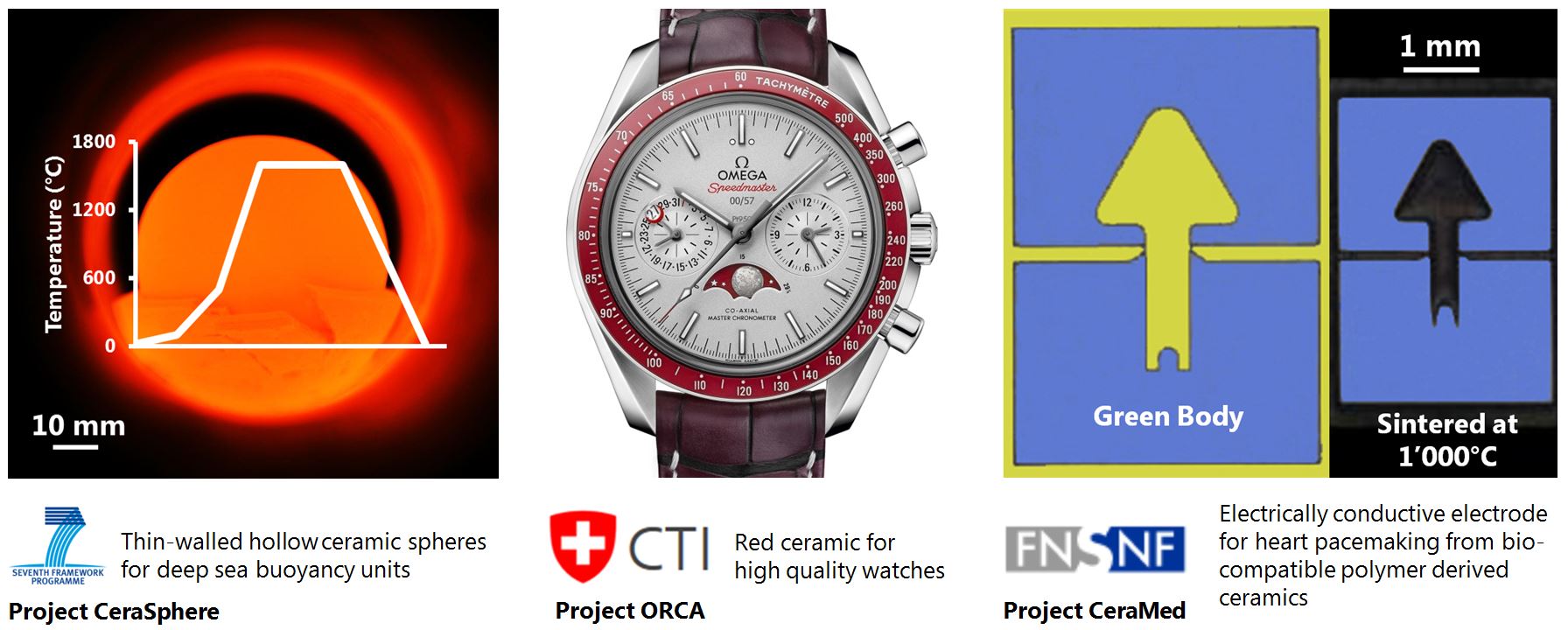
Our recent research activities
Energy, Transportation, Medical and Industrial applications
- Red ceramics for high quality watches
- Lifejackets for deep-sea drills
- High-end brakes for the Cinquecento?
- An innovation in industrial wood cutting
- Electrodes for cardiac pace-makers
- Brennstoffzellen-Heizung wird salonfähig
Processing
- High strength alumina
- Processing and properties of Al/CNF-composites
- Effect of sintering additives on properties of Si3N4/MoSi2
- Healing treatment for defects in dental zirconia
- Pressureless infiltration of MMC
Joining, Design and Properties
- Innovative joining of ceramic materials
- Brazing of Si3N4-ceramic-composite to steel
- Thermo-mechanical stresses in planar SOFCs
- HT oxidation and corrosion of Si3N4-ceramics
- Failure tolerant multi-layer Si3N4-ceramics
- Fracture toughness using the SEVNB method
Services
Scientists:
Dr. Camila P. Canales
Dr. Stefan Heinen
Dr. Heloisa Ramlow
Dr. Tamanna Thakur
PhD Student: