CO2 in construction
Building on CO2
Sophisticated chemical processes can bind climate-impacting carbon dioxide in various forms – and in considerable amounts in the long term. The construction sector, with its massive turnover and huge volumes, is a perfect candidate to making use of them. Empa researchers are working on various processes that give reason for optimism.
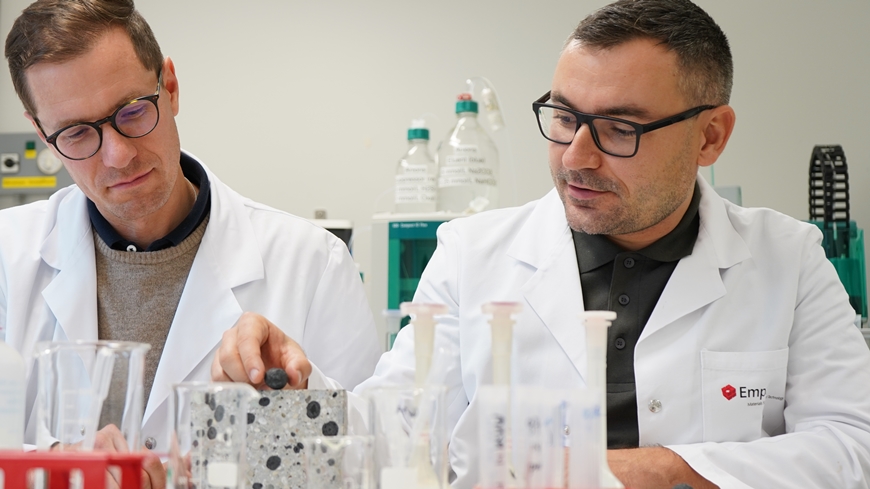
In order to bind CO2 and thus make the construction sector more climate-friendly, experts all over the world are working on new processes – for example, for exhaust vents of factories in the cement industry, which emits large quantities of the greenhouse gas. But what to do with the CO2 once captured? One hope is large-scale underground storage in reservoirs made of porous rock that can store the gas over long periods of time in liquefied form.
Other possibilities are offered by circular economy, especially in the construction sector with its large mass turnovers. CO2 can, for instance, be bound to concrete recycling material using a process known as carbonation to produce new types of concrete. Other chemical processes such as pyrolysis, a heating process under the exclusion of oxygen, of methane to hydrogen – for example for high-temperature industrial processes – yield solid carbon as the final product, which can then be used as a CO2-negative material in the construction industry.
Concrete as a CO2 trap – already in the factory
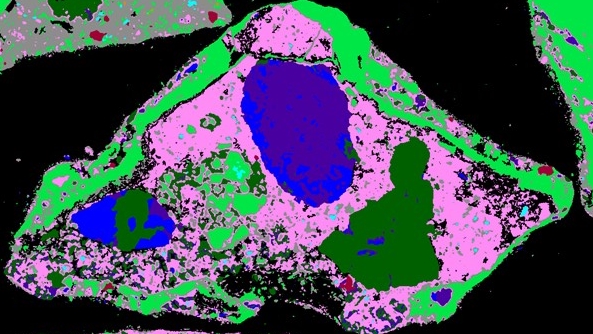
Concrete is capable of re-binding the climate gas emitted during cement production, at least partially. "Carbonation" is the name of this process – a leisurely reaction that takes years and the pace of which depends on numerous factors. The DemoUpCARMA project, led by ETH Zurich, investigated how this process can be used and, above all, accelerated in a concrete plant – in a facility operated by Kästli Bau AG in Rubigen (BE) and using recycled material from concrete structures. The carbon dioxide from a sewage treatment plant was delivered liquefied and converted back into gas at the plant to continuously "flood" the recycled granulate using a process developed by the Bern-based company neustark AG.
Andreas Leemann and Frank Winnefeld from Empa's Concrete & Asphalt lab investigated how efficiently the granulate absorbs CO2. Samples showed clear changes under the microscope: Smaller particles had patches of dark and light portions on the surface where the original cement had changed. Analyses showed that the light portions were calcium carbonate, while the dark phases consisted mainly of calcium silicate hydrate – C-S-H for short – the main product of cement hydration that gives concrete its strength. Carbonation removed some of the calcium from C-S-H: It thus became less calcareous and could in turn react with newly formed cement phases in recycled concrete – with the result that its compressive strength increased.
Tests with concrete types frequently used in Switzerland confirmed these findings. They showed that the process can make concrete more climate-friendly in two ways. Firstly, by absorbing CO2 directly from the atmosphere: in the case of these novel building materials, this absorption can be up to 10 percent of the emissions initially released into the atmosphere during the production of the cement for the original concrete. Secondly, by reducing the cement content in recycled concrete by 5 to 7 percent – thanks to its higher strength. The bottom line, according to the Empa experts, is a CO2 saving potential of a good 15 percent.
When, if and to what extent these results can be applied in practice is, of course, still open – partly because of the question of how well and at what technical and financial expense the process can be implemented in concrete plants.
Biochar as concrete ingredient
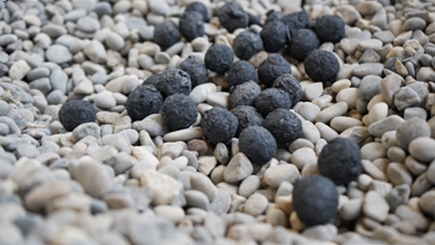
Another team from Empa's Concrete & Asphalt lab is developing a process for integrating plant-based charcoal – biochar – into concrete. This material is produced by pyrolysis of biological material and consists to a very large extent of pure carbon, which the plants had taken up from the atmosphere in the form of CO2 during their growth (in a process called photysynthesis).
While concrete products containing biochar are already on the market – the charcoal is often added to concrete in untreated form, which can lead to problems. "Plant-based carbon is very porous and therefore absorbs not only a lot of water, but also expensive admixtures used during concrete production," says Empa researcher Mateusz Wyrzykowski.
Therefore, the experts suggested processing it into pellets. To produce them, they used a rotary mixer filled with biochar, water and a binder, which yielded pellets with diameters between 4 and 32 millimeters. The researchers used the pellets to produce concrete of strength classes C20/25 to C30/37, which are widely used in building construction and civil engineering.
The resulting carbon footprint: With 20 percent by volume of carbon pellets in the concrete, the team achieved net zero emissions, according to Wyrzykowski – so the amount of carbon contained in the concrete offsets all emissions produced in the production of the pellets as well as the concrete. In the case of lightweight concrete with a density of around 1800 kg/m3, the balance becomes even better: A carbon content of 45 percent by volume leads to negative emissions of minus 290 kg CO2/m3.
In the long term, Empa lab head Pietro Lura sees potential for negative emissions that go far beyond biochar. In a concept pursued by several Empa labs together, synthetic methane is produced in the Earth's sunbelt using just solar energy, water and atmospheric CO2 followed by the subsequent pyrolysis of the gas. "This gives us hydrogen, which can be used in both industry and mobility, and solid carbon, which we can incorporate into concrete – just like biochar," says Lura.
Insulation materials for buildings
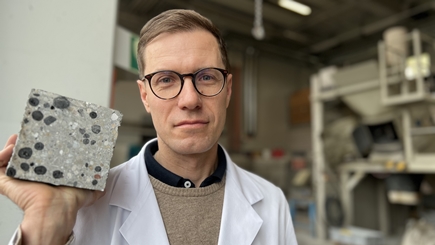
Biochar is also a topic in Empa's Building Energy Materials and Components lab. A team led by Jannis Wernery is developing a new type of insulating material from plant-based raw materials or waste that permanently binds the CO2 it contains and thus acts as a permanent carbon sink. This is a promising idea, especially in view of the great importance of insulating materials in the task of making many buildings more energy-efficient and thus more climate-friendly in the future.
Most of the carbon plants had captured from the atmosphere in the form of CO2 during their growth can be permanently fixed by pyrolysis. The resulting biochar can then be bound in the insulation of buildings throughout their lifetimes. What's more, after demolition of the buildings, the biochar could be brought out on fields, where it would increase the fertility of the soil, yet remain bound for centuries – unlike other plant-based building materials such as cellulose insulation, which release the stored CO2 as it rots.
Of course, there are still many details to be clarified before the material is ready for use. For example, it must be ensured that all the ingredients of the insulation materials are suitable to be used as fertilizer. Moreover, a marketable product would have to be competitive in terms of thermal insulation and, at the same time, guarantee adequate fire protection. According to Empa researcher Wernery, preliminary studies showed that these goals are well within reach.
In the long term, biochar-based insulation materials could significantly improve Switzerland's carbon footprint. According to model calculations, a realistic partial replacement of conventional insulation materials with biochar could save around half a million tons of CO2 equivalents each year – on the one hand through reduced emissions during their production, and on the other through the long-term storage of atmospheric CO2. That would be equivalent to one percent of Switzerland's total greenhouse gas emissions. A project with a huge potential upside that also convinced funding institutions: The Minerva Foundation, the ETH Board and the Swiss Federal Office of Energy (SFOE) are supporting the project, as is the Stadtwerk Winterthur climate fund.
Dr. Mateusz Wyrzykowski
Concrete & Asphalt
Phone +41 58 765 4541
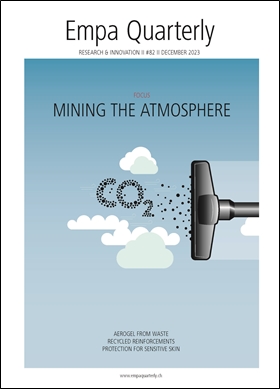
Empa Quarterly#82 Mining the Atmosphere
To limit climate change, we need to compensate not only for future emissions, but also for historical ones. One solution would be the "atmospheric vacuum cleaner": we remove the excess CO2 from the atmosphere. But what do we do with it? Instead of extracting the carbon for polymers, medicines, fibers, fuels and the like from crude oil, we use atmospheric CO2. This is the simple – yet extremely challenging in technical terms – idea behind Empa's new research initiative, Mining the Atmosphere.
Read the EmpaQuarterly online or download the pdf-version.
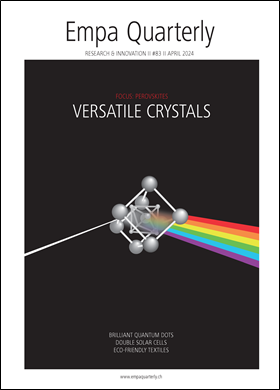
Empa Quarterly#83 Perovskites: Versatile cristals
Over 180 years ago, a curious crystal was discovered in the Ural Mountains. Today, it has given rise to an entire class of materials that is of great interest to researchers: perovskites. What all perovskites have in common is their crystal structure, which gives them unusual properties. By changing the exact composition of the perovskite, scientists can control these properties. Empa researchers are using this promising material to develop solar cells, detectors and quantum dots.
Read the EmpaQuarterly online or download the pdf-version.
-
Share

Packaged in beer Empa researchers have extracted nanocellulose from a waste product of beer brewing and processed it into an aerogel. The high-quality biodegradable material could be used in food packaging. |
Beyond Zero A set of innovations from the Empa labs that are strongly CO2-reduced and even CO2-negative, are going to be installed and analysed inside a new unit at NEST, the innovation building of Empa and Eawag. |