Sprint, a new NEST Unit now in operation
Demolition and breakthrough
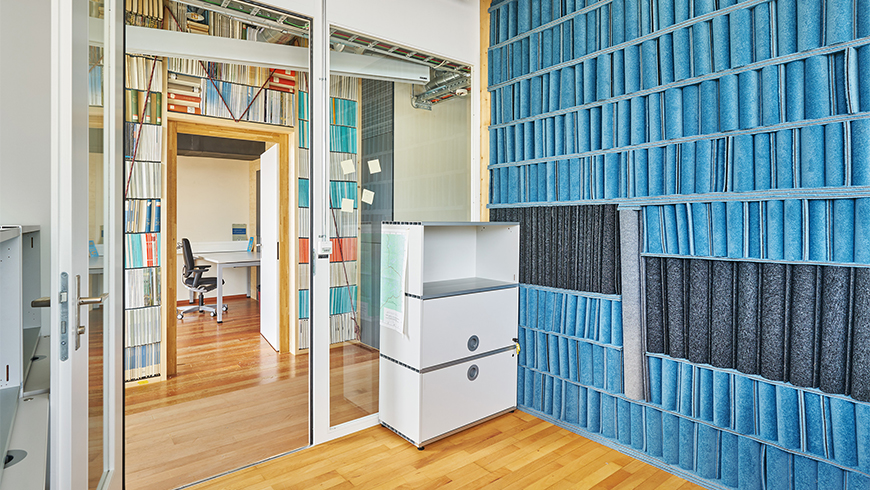
Rethinking planning, execution and management
Building with reused materials is an iterative process, in which the question of available materials runs through the entire construction process. In order for such a project to be implemented in the shortest possible time, it requires, among other things, a rethinking of planning and execution, as well as a flexible schedule. "The time factor is always a big challenge in reuse, as the reused material must be found in a timely manner and also be available exactly when needed. Contrary to our initial concerns about the tight schedule, we were able to find the re-use materials even faster than new materials. This is mainly due to the current scarcity of resources – but also shows that re-use has no impact on construction time," explains Kerstin Müller, architect and member of the management team at baubüro in situ, which planned the Sprint unit.
Building with reused materials also requires a different mindset when it comes to understanding economic efficiency. The added value of re-use clearly lies in the fact that the material is given the necessary respect. Hans Emmenegger, head of the carpentry division at HUSNER Holzbau, sees great opportunities in this: "In my opinion wood, for instance, is a very grateful raw material. It can be processed well, which in turn makes it easy to reuse. If wood is installed in a healthy way, i.e. dry, it does not lose value. On the contrary, it actually gains value because of its characteristic aesthetics."
Reuse as a booster for innovation
Building with reused materials requires not only flexibility in planning and execution, but also more flexibility in design. For example, planners must be aware that the material they find will partly determine the final design. "Sprint impressively demonstrates that reused material is by no means a hurdle to design, but that creativity can be used to achieve design elements that one would not have thought of initially. The different partition walls in Sprint are a great example of this. We built some from scrap bricks, others from old books, and still others from old carpet," says Oliver Seidel, architect and member of the management team at baubüro in situ.
The carpet partition for Sprint, for example, was developed by Jonas Schafer, component hunter at baubüro in situ. It can be completely dismantled after use. Empa researchers tested the wall for airborne sound insulation in the acoustics lab. The carpet partition has proven itself in terms of its building acoustics properties and is now being put to the test in the Sprint offices (see box).
Exploiting opportunities and accepting limits
Sprint shows that reuse is not cheaper per se in today's market situation. However, Oliver Seidel is convinced: "As soon as a competitive market with reused materials and components has established itself, cost advantages will also accrue for reuse. Moreover, I believe that there is a need for CO2 taxes, for example, which would increase the prize of new materials and relieve the costs for used materials, so that their ecological benefit can be quantified."
Reuse also offers new opportunities. For example, certain reused materials such as natural stone or automatic fire protection doors suddenly can become affordable, as opposed to the same components, brand-new. What's more, the materials can be evaluated in terms of the CO2 savings they enable.
For other materials such as pumps, valves and other technical components, the question arises as to whether reuse is worthwhile in terms of warranty and service life. It is quite possible that it makes more sense to procure these components anew. Verifying the service life of such engineered components is feasible, but time-consuming and costly. "The challenge in building with reused materials is to find a balance between what is technically feasible and what makes sense," says Maike Stroetmann, BIM CAD department manager at Bouygues Energies & Services.
More information on building with reused materials is available on the Sprint website.
Design for Disassembly
Re-use material tested for use in building acoustics
Empa researchers tested the airborne sound insulation of the carpet partition specially designed for Sprint in the acoustics lab. For this purpose, the partition wall was set up in an adapter between two test rooms and the airborne sound transmission was measured. The weighted sound reduction index (Rw) was calculated from the frequency-dependent measurement data.
With several measurements, the researchers investigated how the carpet tiles must be folded for optimal sound insulation. In the best case, the researchers achieved a sound insulation of 26dB. This means that, as a room divider, the carpet wall achieves much better acoustic insulation than, for example, mobile movable walls in open-plan offices. The results show that this innovative and circular partition has potential wherever buildings are designed to be flexible or even temporary, e.g. in modern interim uses such as popup stores, restaurants and the like.
-
Share