Revolutionizing energy technology
Scalable supercapacitor technology made from graphene
Supercapacitors, or supercaps in short, are fast, powerful energy storage devices. They complement the relatively slow (dis-)charging batteries in numerous applications ranging from electric cars to industrial machines and wind turbines. A team of Empa researchers wants to develop better supercaps based on graphene – and make them ready for large-scale commercial production.
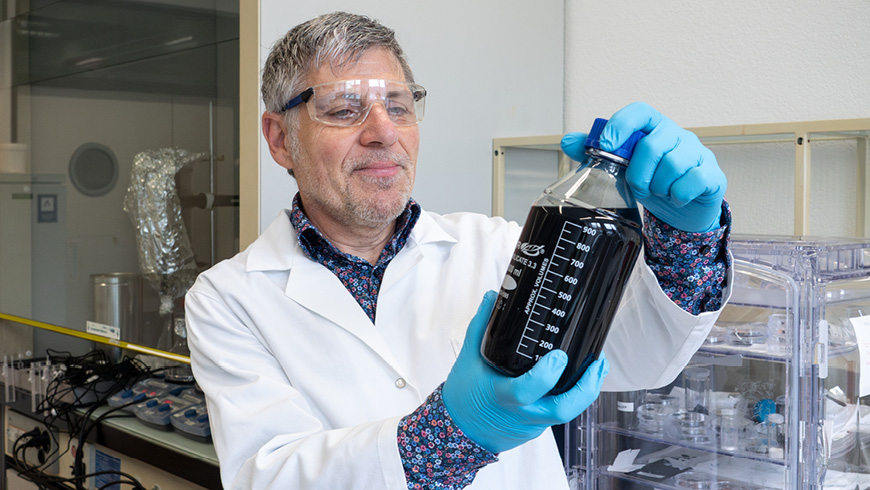
Supercapacitors are the nimble little siblings of batteries. Both technologies store electrical energy. Batteries have a high energy density but a low power density. In other words, they can store a lot of energy, but charging and discharging is rather slow. Supercapacitors are pretty much the opposite: They absorb and release energy at lightning speed but can only store a small amount of it.
“Batteries are like a large container with a narrow neck that can only fill up slowly. Supercapacitors are more like small cups with a wide opening. They fill up quickly, but have little volume,” explains Empa researcher Sina Azad. The two technologies are often teamed up: In an electric car, supercaps quickly capture the braking energy and then pass it on to the slower batteries for storage. Supercaps can also be found in solar farms and wind turbines, as well as in industrial machines that sometimes need a lot of electricity quickly.
Azad, a postdoctoral researcher in Empa's Functional Polymers laboratory, and his team have set themselves the goal of improving these ubiquitous, fast storage devices by developing a new kind of electrode based on graphene. This two-dimensional form of carbon should allow the supercaps to achieve significantly higher energy densities.
“Record energy densities for supercapacitors have been described several times in the scientific literature,” Azad acknowledges. The focus of his research project is not record-breaking, but scalability. Right from the start, the researchers are focusing on materials and processes that can be implemented not only in the laboratory but also on an industrial scale. For this reason. their project is being supported by Bridge, a joint funding program of the Swiss National Science Foundation (SNSF) and Innosuisse.
The surface matters
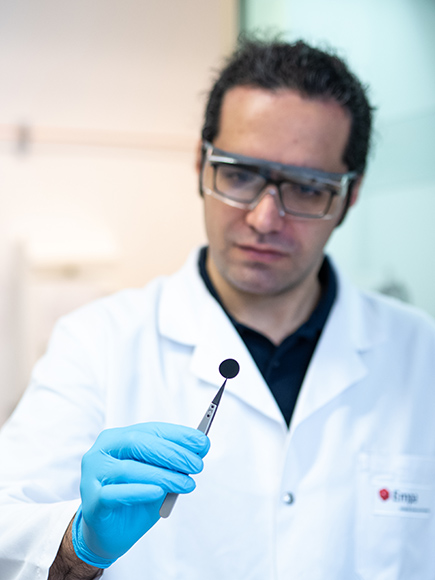
Similar to a battery, a supercapacitor consists of two electrodes surrounded by a liquid electrolyte. During charging and discharging, the electrolyte transports the ions – the charge carriers – from one electrode to the other. Unlike in a battery, however, no chemical reaction takes place. “Supercapacitors store energy electrostatically by depositing as many charged particles as possible on the surface of the electrode,” says Jakob Heier, head of the Functional Thin Film Solution Processing research group in the Laboratory for Functional Polymers, to which Sina Azad belongs.
Hence, the larger the surface area of the electrode, the more ions can attach to it – and the higher the energy density of the supercapacitor. “Today, highly porous activated carbon is usually used as the electrode material of choice,” says Empa researcher Vahid Charkesht. However, in contrast to graphene, activated carbon has a very low electrical conductivity, which impairs the storage capacity of the electrode.
Another disadvantage arises during the processing of the material. In industry, the electrodes are printed onto flexible films in a roll-to-roll process, then cut and rolled up into finished supercaps. To be able to print the powdered activated carbon onto a carrier material, it is mixed with binding agents and other additives that impair its porosity.
From ink to product
Printing graphene is not a given either. Pure graphene for industrial applications is usually obtained from graphite. Conventional production methods have a very low yield of pure graphene, which has to be separated from waste products at great expense. However, thanks to a previous research project, the Empa researchers have an ace up their sleeve: They developed a process with which high-quality graphene can be “exfoliated” from graphite both cost-effectively and efficiently, and processed into a gel-like printable ink.
This graphene ink offers a decisive advantage in the production of supercapacitor electrodes. By cleverly mixing two different types of graphene, the researchers can selectively influence the size of the pores between the graphene layers. “If the pore size of the electrode is matched to the size of the ions in the electrolyte, the energy density of the supercapacitor increases dramatically,” explains Azad. With activated carbon, controlling pore size is impossible.
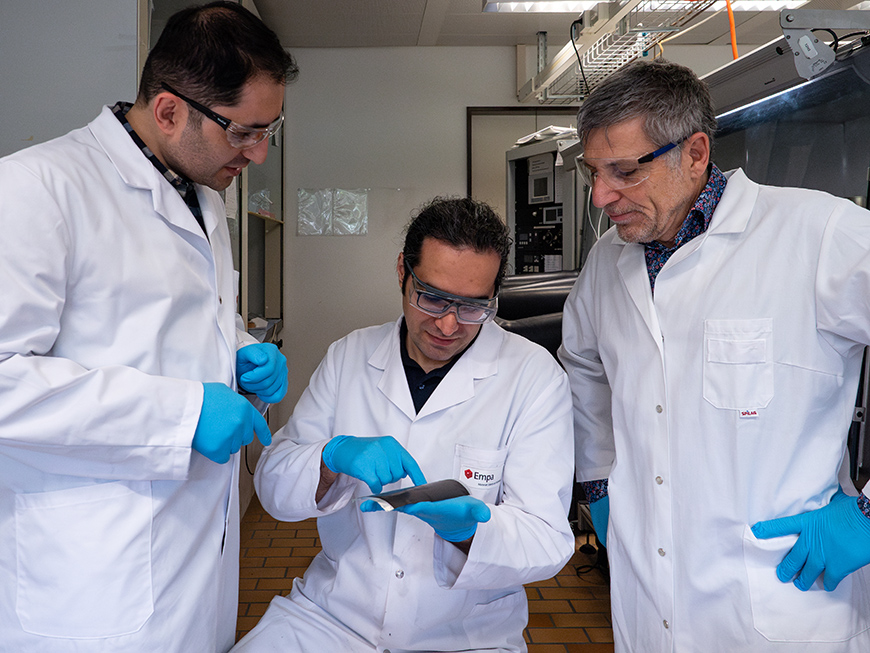
With their high conductivity, precise pore size, large surface area and scalability, the new electrodes are likely to become a high-tech product. “At the end of the project, we want to bring our technology to market, either with industrial partners or with our own spin-off,” says Jakob Heier.
However, there is still a lot to do – the project runs until 2028. The researchers not only want to develop the electrode technology, but also manufacture electrodes and install them in functional prototypes. The aim is to define the right process steps, find a suitable electrolyte and then precisely characterize the finished supercaps. “We want to develop a real, reliable product,” summarizes Azad.
Dr. Sina Azad
Empa, Functional Polymers
Phone +41 58 765 66 50
Dr. Jakob Heier
Empa, Functional Polymers
Phone +41 58 765 43 56
Surfaces and Interfaces
Totally superficial? You bet! What might be a bit of a character flaw in a person is actually a good thing in materials science. Because, chemically speaking, it's what happens on the surface that counts. A sound understanding of surfaces and interfaces enables everything from better electronics to more robust bridges. Whether it's biological compatibility in implants, antibacterial coatings in hospitals, or catalytic processes in the production of synthetic fuels – surfaces are crucial to all of these.
Read the latest EmpaQuarterly online or download the PDF version.
-
Share