Circular economy
Fluorine recycling for lithium-ion batteries
Lithium-ion batteries contain salts rich in fluorine, which decompose in humid air to toxic, highly corrosive hydrogen fluoride. The hazardous nature of this substance makes recycling more difficult and more expensive. A research project entitled "Fluoribat" is now being launched at Empa to solve this problem. This could help to make the life cycle of a rechargeable battery less expensive and at the same time safer.
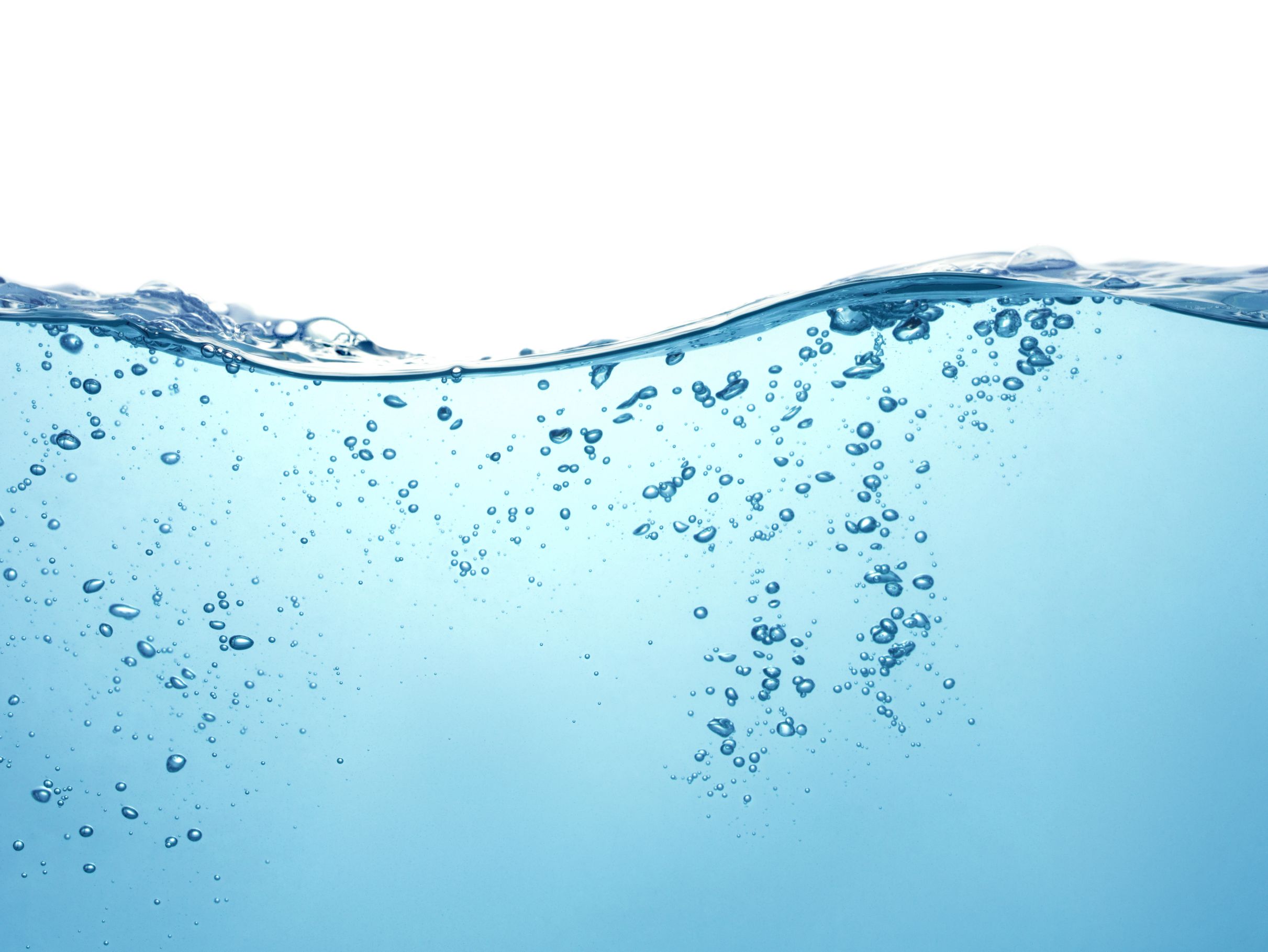
Batteries are ubiquitous. The Global Battery Alliance of the World Economic Forum WEF expects the number of batteries for electric mobility and stationary storage applications to increase tenfold within the next ten years. Lithium-ion batteries will account for the largest share of this growth.
A blessing and a curse
Due to the large volume of batteries that will have to be manufactured and recycled in the coming years, a chemical element is coming into focus that has rarely been discussed so far: fluorine. It is found - in small quantities - in all lithium-ion batteries. The electrolyte liquid of such a battery contains hexafluorophosphate anions PF6- - a fluorine compound that ensures the long-term stability of the battery and enables high cell voltages. The disadvantage: PF6- decomposes in contact with water or in humid air to toxic, highly corrosive hydrogen fluoride HF. This means that whilst the battery is in operation, it has to be packaged in an airtight envelope, otherwise it will emit toxic fluorine compounds. During recycling at the latest, the airtight envelope is slit open. The resulting hydrogen fluoride makes the recycling process complicated and expensive.
The goal: waterproof fluorine salts
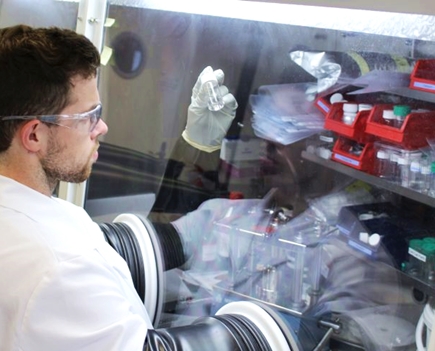
Empa is starting a research project called "Fluoribat" in the summer of 2020 to address this issue. The research team of Corsin Battaglia, head of the laboratory "Materials for Energy Conversion", has developed a new, non-flammable water-based electrolyte for lithium-ion batteries which is compatible with electrode materials already in use in these batteries. "Our cells still show more than 80% of their initial capacity after 200 charging and discharging cycles," says Maximilian Becker, battery researcher in the laboratory of Corsin Battaglia. The water-stable lithium salt used in Empa's experimental battery cells can be manufactured on a large scale at competitive prices.
For successful commercialization, the long-term stability of the battery needs to be improved further. However, if this hurdle can be overcome, such a battery could be produced and recycled at much lower cost - an absolutely dry environment is then no longer necessary for either of these steps.
Towards a circular economy
At the same time, water-based recycling of end-of-life lithium-ion batteries opens up new opportunities for a circular economy. If the electrolyte salts can be easily recovered from batteries, the fluorine they contain can be used for new batteries - an increasingly important aspect in view of the expected quantity of batteries. Empa's "Technology and Society" Laboratory, headed by Patrick Wäger, specializes in the recycling of batteries and calculating the environmental impact of new technologies along their life cycle. The analysis is intended to assess the advantages of batteries based on water-resistant fluorine salts. In the study, this new generation of batteries will be compared with batteries of the current generation with regard to safety and environment.
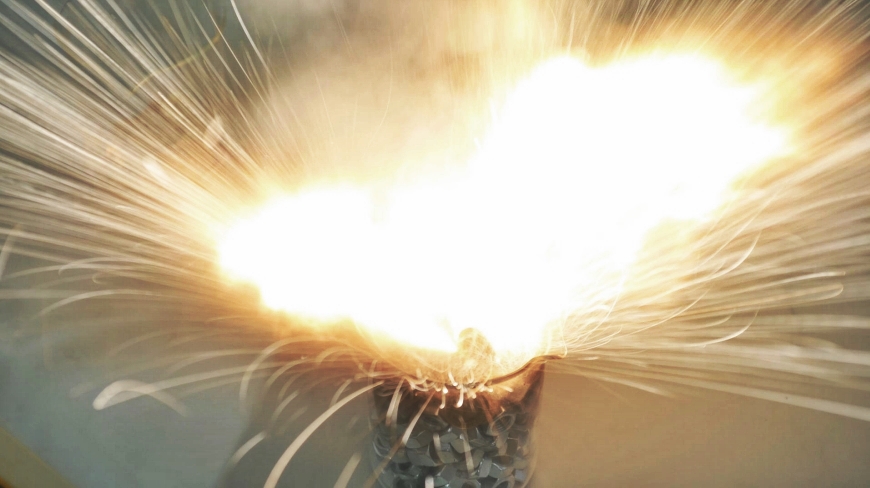
Battery research in the European framework
Dr. Corsin Battaglia
Materials for Energy Conversion
Phone +41 58 765 41 31
Dr. Patrick Wäger
Technology and Society
Phone +41 58 765 78 45
patrick.waeger@empa.ch
-
Share