Ultra-thin yet strong against noise
A filigree sound absorber for all weathers
Empa researchers have developed innovative sound absorbers made of mineral foams. Not only are they significantly thinner than conventional materials, they can also be designed specifically for different frequencies. They have now been tested for the first time in a driveway in the city of Zurich to dampen street noise.
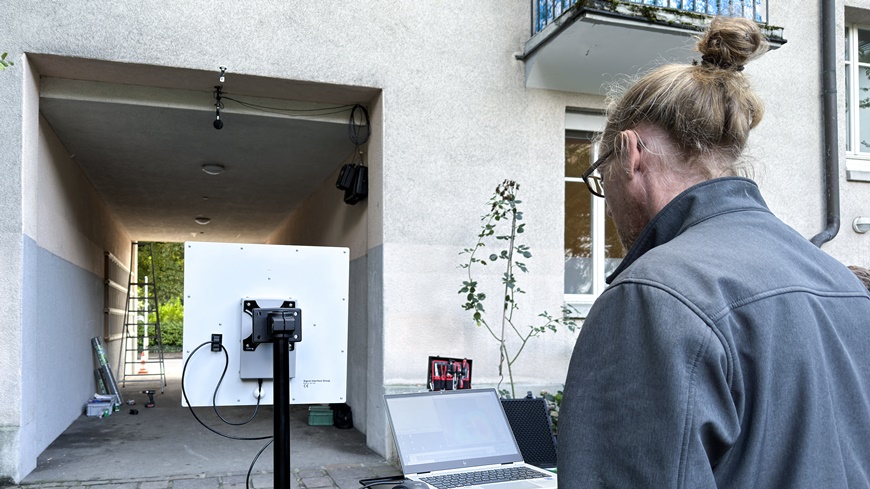
In the fight against noise, every centimeter counts in the construction sector. Traditional sound absorbers are usually made of bulky materials such as rock wool or melamine foam, however. In order to effectively dampen even low sound frequencies, thick layers of insulation materials are required – which costs space, restricts design and is often simply not even feasible in outdoor areas. Together with the company de Cavis, Empa researchers have therefore developed ultra-thin sound absorbers made of mineral gypsum or cement foams. These are just as effective as conventional absorbers, but around four times thinner. Further advantages: The foams can be tuned to specific frequency ranges and are easy to cut and install. Made from plaster or cement, they can be fireproof and recyclable, and do not release any harmful particles. Cement foams are also weatherproof and therefore suitable for outdoor use.
A labyrinth for sound waves
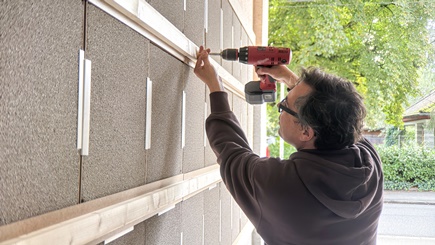
According to Empa researcher Bart Van Damme, the high sound absorption despite the low thickness is based on a patented design: “The varying pore structure of the mineral foams forces air particles to take a longer route to get into the material and out again. Despite the low thickness, this creates the impression of a much thicker absorber for the sound waves.” The decisive factor here is having the largest possible pores with the thinnest possible pore walls. The researchers from Empa's Acoustics/Noise Reduction lab use several porous layers for the new type of sound absorber. They not only vary the thickness of the individual layers and the size of the pores but also provide them with tiny holes. While the foams, which have a pore content of over 90 percent, can be produced from plaster or cement using established processes, perforation is currently still done by hand.
The researchers also used a numerical model to simulate how air flows through the pores of the mineral foams at the smallest level. “We can thus simulate and even specifically influence the acoustic behavior of the entire material by varying pore size, perforation and layer structure,” says Van Damme.
Tailor-made instead of bulky
Traffic noise is typically in the range between 500 and 1000 Hertz. Model calculations show that four coordinated layers of fine-pored mineral foam with a total thickness of around 5.5 centimeters are sufficient as insulation material for this frequency range. An initial prototype with a total area of twelve square meters has already been tested in a driveway together with the city of Zurich. In the preliminary simulation of the driveway, the researchers optimized the arrangement of the individual panels on the walls. Controlled measurements on site confirmed the predictions: The noise level dropped by up to 4 decibels thanks to the 72 panels. The effect was particularly noticeable for passing cars approaching or leaving the driveway, as the sound is reflected several times by the panels on the way into the courtyard.
A comparison with conventional rock wool showed that the new absorbers are more reliable at low frequencies and slightly less efficient at higher frequencies – but still reduce sound transmission in the area of peak absorption. “Even an installation as compact as the one in the driveway significantly reduces noise,” concludes Van Damme.
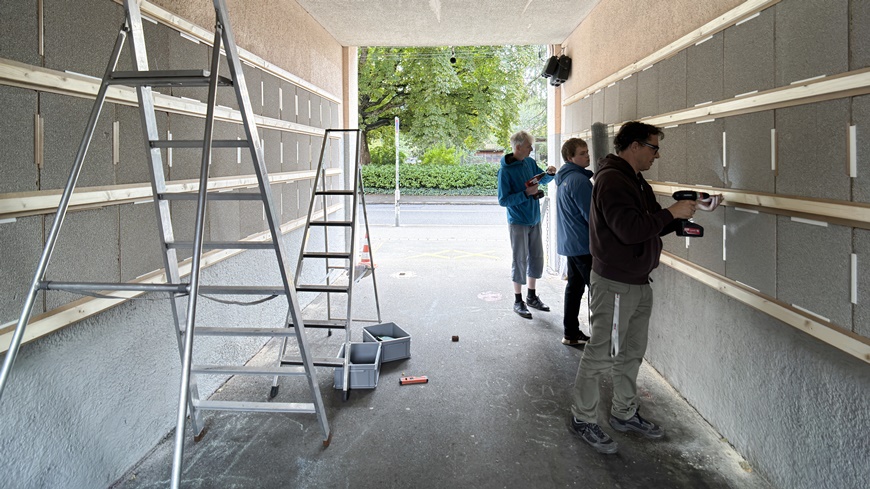
Predestined for special applications
In future, the mineral sound absorbers could be retrofitted in driveways, under balconies or on façades in noisy streets. As with all open-pored absorbers, the prerequisite is protection from the weather and from dirt, for example with a perforated top layer. “Ideally, absorbers are already taken into account in the architectural design of new buildings,” explains Van Damme. The elements can also be easily integrated into stairwells or large interior spaces such as offices, canteens or sports halls – also from a design perspective, as the porous mineral foam is made of the same material as the surfaces of the walls.
According to Bart Van Damme, the idea for the absorber originated several years ago. However, the breakthrough only came through the combination of material development and acoustic modeling as part of an Innosuisse project. Thanks to the modeling, the absorber can now be flexibly customized: Should it dampen particularly low tones, such as in large halls? Or should it be more effective in the mid-range, such as in traffic noise, offices or classrooms?
At the moment, production is still complex and partly done by hand. Together with a suitable industrial partner, the material is now to be further developed and produced on a larger scale. The potential is huge – especially for special applications where limited space, fire protection and design requirements have to be taken into account at the same time.
Dr. Bart Van Damme
Laboratory for Acoustics / Noise Control
Phone +41 58 765 4110
Surfaces and Interfaces
Totally superficial? You bet! What might be a bit of a character flaw in a person is actually a good thing in materials science. Because, chemically speaking, it's what happens on the surface that counts. A sound understanding of surfaces and interfaces enables everything from better electronics to more robust bridges. Whether it's biological compatibility in implants, antibacterial coatings in hospitals, or catalytic processes in the production of synthetic fuels – surfaces are crucial to all of these.
Read the latest EmpaQuarterly online or download the PDF version.
-
Share