New materials for electrolysis
Making green hydrogen more affordable
Green hydrogen – produced from water using renewable energy – is an important sustainable fuel and energy storage medium. However, its industrial production is significantly more expensive than the conventional production of hydrogen from fossil sources. Empa researchers and their partners are developing materials for water electrolysis that are not only efficient and more cost-effective but can also be scaled up to an industrial level.
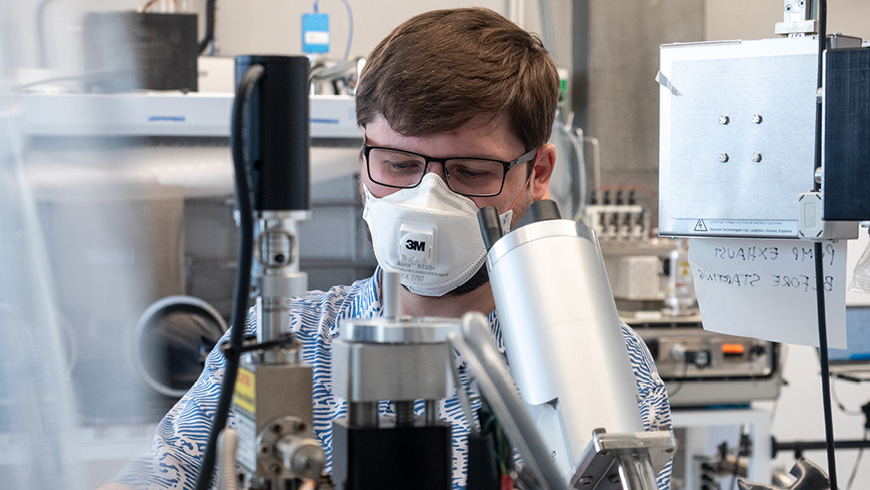
Hydrogen can partially replace fossil fuels, which makes it a cornerstone of the energy transition. The idea is simple: electricity from renewable sources plus water equals hydrogen and oxygen. If the hydrogen is burned as fuel, it reacts with atmospheric oxygen to form water, and the cycle is complete – without any greenhouse gas emissions.
At least that's the ideal scenario. In reality, the production of “green” hydrogen using electrolysis faces strong competition. Over 90 percent of this hydrogen is currently obtained from fossil sources, mainly from natural gas. The main reason for this is that the more sustainable hydrogen from electrolysis is around twice as expensive to produce.
In a project supported by the Swiss National Science Foundation (SNSF) and the French Agence Nationale de la Recherche (ANR), Empa researchers from the Materials for Energy Conversion laboratory want to change this. The materials used in electrolysers are one of the cost drivers in electrolysis. Together with researchers from the French research institutes French Corrosion Institute in Brest and LEMTA in Nancy, Empa researchers are working on more affordable alternatives for two key components of electrolysis devices.
Resisting corrosion
The researchers are focusing on proton-exchange membrane water electrolysis, or PEMWE for short. PEMWE electrolysers are efficient and compatible with the energy fluctuations that can be expected from renewable sources. However, the environment inside the electrolyser is corrosive. In the core of the electrolyser, steel simply dissolves “like sugar in a cup of tea”, says Empa researcher Konstantin Egorov. And even parts that do not come into contact with the highly acidic core corrode. Even minor quantities of metals dissolved in the ultra-pure water flowing into the device in order to be electrolyzed impair its performance and durability.
Components for transporting water and the resulting gases within the electrolyser are therefore made of titanium, which is both expensive and difficult to process. But even that is not enough: To prevent the titanium from oxidizing and reducing the effectiveness of the device, the components must be coated with the precious metal platinum, which further increases the costs.
Material scientist Egorov is looking for a way to replace the costly platinum coating while still providing the necessary protection from corrosion. For this, he is using a special form of titanium oxide known as highly crystalline oxygen-deficient rutile. This oxide is missing oxygen atoms in certain places, which gives the material good conductivity while its highly crystalline structure results in high corrosion resistance – exactly the right prerequisites for PEMWE electrolysis. The researchers are also replacing the titanium carrier material with steel. "Besides being more cost-effective, steel components are much easier to manufacture, which allows engineers to create more advanced designs that enhance cell performance", explains Egorov. Thanks to the robust coating, the corrosive environment should no longer be able to harm the material.
Thinking of industrial production right from the start
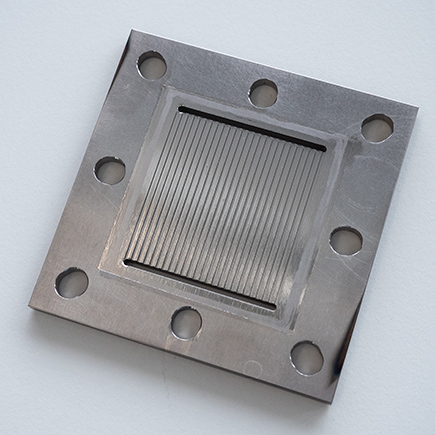
The first results show the high corrosion resistance of the innovative coating. “We were able to develop a method to coat the first component of the PEMWE electrolyser, the so-called bipolar plate, successfully with titanium oxide,” says Egorov. The method the Empa scientist is using is called physical vapor deposition (PVD) and is widely used in industry. “It is important for us to develop something that industry can actually use,” emphasizes the researcher.
The components that Egorov manufactures at Empa are subjected to thorough corrosion tests by his partners, first under lab conditions and then in a functioning electrolyser. The bipolar plate has already successfully passed the tests. Next, the researchers want to coat another key component with titanium oxide, the so-called porous transport layer.
“Coating porous materials poses many challenges,” says Egorov. The pores must be coated evenly so that the underlying material does not corrode – but at the same time they must not become blocked. The coating expert is confident that this can be achieved. The project will run until 2026, after which the Empa researchers hope to bring in industrial partners to develop the innovative technology towards commercialization.
Dr. Konstantin Egorov
Empa, Materials for Energy Conversion
Phone +41 58 765 65 19
Dr. Meike Heinz
Empa, Materials for Energy Conversion
Phone +41 58 765 65 42
Surfaces and Interfaces
Totally superficial? You bet! What might be a bit of a character flaw in a person is actually a good thing in materials science. Because, chemically speaking, it's what happens on the surface that counts. A sound understanding of surfaces and interfaces enables everything from better electronics to more robust bridges. Whether it's biological compatibility in implants, antibacterial coatings in hospitals, or catalytic processes in the production of synthetic fuels – surfaces are crucial to all of these.
Read the latest EmpaQuarterly online or download the PDF version.
-
Share