Empa participating in «ADMACOM», a major new EU project
Combination is simple – joining poses the greater challenge!
Oct 21, 2013 | REMIGIUS NIDERÖST
On 1st October a large-scale EU project called «ADMACOM», in which Empa is taking on a significant role, kicked off. The aim is to find out how components (such as aircraft parts) which are manufactured using a combination of various materials can be economically produced, without the need to accept reduced functionality or security.
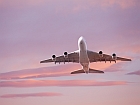
Source: iStockPhoto.com |
|||
Faster, cheaper and bigger are the new watchwords! A wide range of developments made over recent years would not have been possible without modern technologies and new materials. The automobile industry, for example, is relying on concepts involving lightweight structural techniques in order to replace steel and other metals as far as possible in new cars. The aim is to reduce weight so as to minimize fuel consumption or increase range in the case of electric vehicles. The largest passenger aircraft in the world, the Airbus A380, with its 500 seat capacity, would not be able to take off if it were built solely of “classical” materials, due to their enormous weight. Lightweight construction techniques using steel have been exploited more or less to the end of their potential, creating demand for new materials and assembly methods. Examples of these new products include carbon fiber reinforced polymers (CFRP) and composite materials of various kinds. In the case of the A380 the necessary weight reduction was achieved by the use of fiber reinforced polymers and sandwich construction techniques. The fuselage skin is only made of pure aluminium on the underside of aircraft – the upper two thirds are made of glass fiber reinforced aluminium material. | |||
Innovative material combinations – not solely advantageous The advantages offered by modern materials are well known. CFRPs are extremely strong, corrosion resistant and lightweight. The combination of different materials of which the composites are made enhances the positive characteristics of each individual component. Certain metals are known for their toughness, thermal conductivity and good working characteristics and these can be advantageously combined with ceramic fibers known for their stiffness, strength and low temperature coefficient. In the case of synthetic materials, properties such as plasticity, hardness, elasticity, fracture strength and thermal and chemical resistivity can actually be “selected” by a suitable choice of starting materials, manufacturing process and additives. |
|||
|
|||
|
An electromagnetic actuator made of a combination of different materials: steel and metal alloys, ceramics and ceramic matrix composites. To create a functioning device from this combination of materials is the challenge facing the EU’s «ADMACOM» project. | ||
|
|||
The idea of combining several materials to create a single part, with the aim of accumulating and enhancing the positive characteristics of the individual components, is a seductive one. In practice, however, materials cannot be simply combined at will since their properties – expansion or shrinkage, mechanical strength, electrical and thermal conductivity, and so on – often differ enormously. These differences make certain material combinations difficult or even impossible to achieve, and often even joining such materials is a challenge. Whilst, for example, with a classical material such as steel several individual components can be welded together, with ceramics and polymers this is not possible so other joining and connection techniques such as soldering or the use of adhesives must be considered. These methods are, however, often unproven for applications with novel materials. | |||
An EU project with prominent partners This is exactly the point at which the «ADMACOM» project (Advanced Manufacturing Routes for Metal/Composite Components for Aerospace) takes up the baton. This large-scale 7th EU Framework Program project, which began in October, is funded to the tune of €4 million. Both Empa's High-Performance Ceramics Laboratory and its Joining Technologies and Corrosion Laboratory are actively involved in the project and are engaged in developing and manufacturing an electromagnetic actuator of the kind used in aircraft or space vehicles to position aerodynamic control surfaces or for similar applications. |
|||
|
|||
The project website can be found at: http://cordis.europa.eu/projects/rcn/108897_en.html | |||
|
|||
|
|||
|
|||