Le verre résiste aux chocs
Incassable
Le verre peut-il fluer aux tempéra- tures ambiantes et résister ainsi aux chocs? C'est ce que prédisait une théorie des années 70. Des chercheurs de l'Empa en ont maintenant apporté la preuve. Ce résultat pourrait permettre d'imprimer des microstructures de verre en 3D.
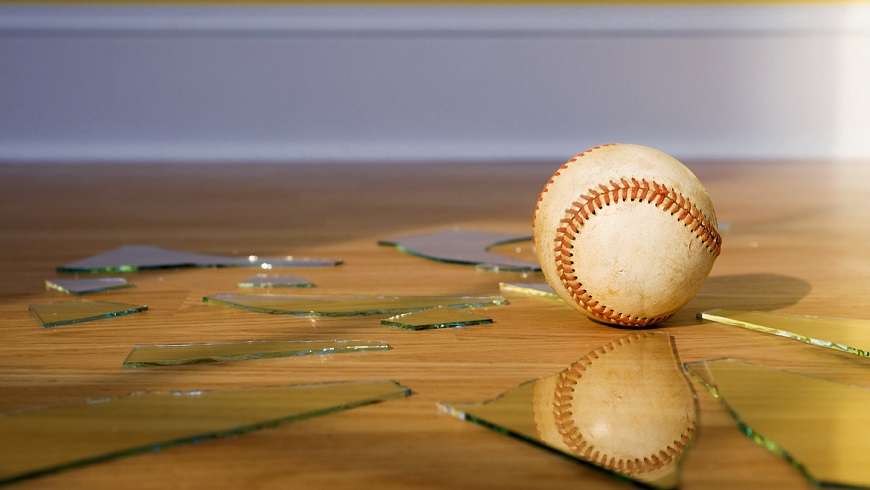
Ce que nous avons mesuré, personne au monde ne l'avait encore vu», remarque Rajaprakash Ramachandramoorthy. «Nous avons beaucoup mieux compris la manière dont le verre se brise que quiconque auparavant.» Raj, comme ses collègues l'appellent, travaille au laboratoire de «Mécanique des matériaux et nano- structures» sous la direction de Johann Michler.
L'équipe scrute les propriétés du matériau aux plus petites échelles. Des machines de leur conception impriment à l'aide de minuscules tampons une pression sur des microcolonnes fines de quelques microns. Ils observent ensuite au microscope électronique comment ces micro- colonnes se brisent sous ces forces mesurées avec la plus grande précision. Forts de ces résultats, les chercheurs peuvent se prononcer sur la structure intérieure du matériau.
Une longue pression et marteler
Ramachandramoorthy et son collègue Jakob Schwiedrzik ont utilisé cette méthode pour étudier le verre quartzeux. Ils lui ont découvert des propriétés bien éloignées de celles que nous connaissons au niveau macroscopique. Lorsqu'il subit une pression lentement croissante, le verre se com- porte comme du mastic. Si la pression croît un peu plus vite, il peut se déchirer et éclater. Et lorsqu'on lui imprime de très brèves impulsions, il se montre à nouveau visqueux et déformable. «Notre essai en com- pression le plus long a duré environ 20 minutes, explique le chercheur. Nos impulsions les plus rapides sur les microcolonnes n'ont duré que 100 microsecondes, comme un coup de marteau».
Les prévisions des années 70 confirmées
Ces recherches conduites à l'Empa ont fourni les premières données expérimentales sur certaines propriétés du matériau qui, jusqu'alors, n'avaient été que postulées. La déformabilité des matériaux amorphes tels que le verre avait été indépendamment prédite à la fin des années 70 par le physicien Frans Spaepen de l'Université de Harvard et, quelques encablures plus loin, par Ali S. Argon du «Massachusetts Institute of Technology» (MIT). Les deux théories, que nous nommerons ici «du verre fluant», pointent dans la même direction: pour la fabrication de systèmes micromécaniques non cassants, le verre est préférable au silicium. Il résiste à des forces supérieures.
Cela n'avait pourtant jamais pu être prouvé expérimentalement. On ne savait soumettre les échantillons microscopiques qu'à des pressions lentement croissantes. Au niveau macroscopique, les expériences dynamiques à haute vitesse provoquent une onde de choc qui l'emporte sur les mécanismes de déformation. Se passe alors ce que nous connaissons tous: le verre se brise dès que l'onde de choc croise un défaut, ce qui est pratiquement toujours le cas sur de grandes pièces.
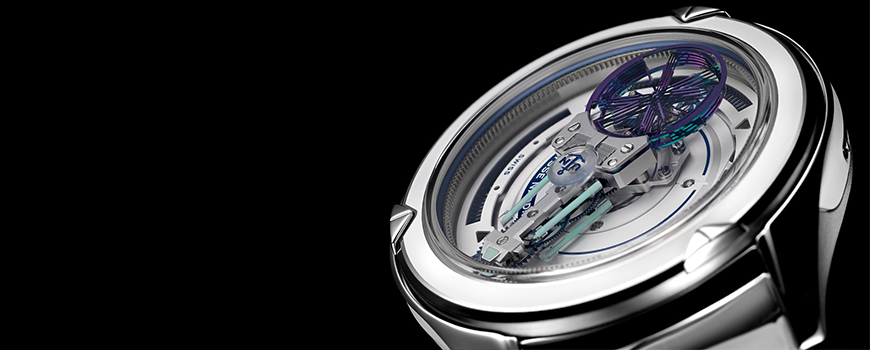
L'expérience ne peut réussir qu'avec la microcolonne
Ramachandramoorthy et Schwiedrzik ont trouvé le moyen de prévenir ce phénomène en utilisant des microcolonnes de verre si menues qu'elles peuvent être statistiquement libres de tout défaut susceptible de fausser les résultats. Et l'onde de choc ne fait plus problème car elle se propage si rapidement dans le microéchantillon que son effet ne se superpose plus au coup de marteau qui déplace les atomes du verre. Il est maintenant possible d'étudier les deux effets séparément. Ce qui a permis de confirmer expérimentalement la quadragénaire théorie du verre fluant de Spaepen et Argon.
Pièces d'horlogerie en verre par impression 3d
Les travaux poursuivis à l'Empa ont déjà attiré l'attention de l'industrie horlogère suisse et de fabricants de microsystèmes électromécaniques (MEMS). Ils pourraient servir de base à l'impression 3D de microéléments de verre pour montres ou instruments de mesure antichoc. En mars 2019, la marque suisse de montres de luxe Ulysse Nardin a déjà présenté un prototype de nommé «FREAK neXt» équipé d'une aiguille des minutes lumineuse en verre. L'aiguille, traversée d'un tube capillaire empli d'un liquide fluorescent, a été imprimée en 3D par l'entreprise suisse spécialisée Femtoprint. Passer du prototype exposé en vitrine à la production en série de montres résistant aux chocs va encore nécessiter quelques efforts de développement. Les chercheurs de l'Empa vont en poser les bases.
L'industrie du verre frappe à la fenêtre
Rajaprakash Ramachandramoorthy est bien occupé et constate déjà que ses travaux n'intéressent pas que l'industrie horlogère. Au lendemain de la publication des résultats sur le verre quartzeux, plusieurs fabricants de verre flotté et de verre boraté l'ont contacté. Ils souhaitent tous mieux connaître les micropropriétés de leurs produits. De nouveaux projets de recherche sont déjà lancés.
«Notre méthode permet en principe d'étudier tous les systèmes à base, entre autres, de matériaux amorphes, métaux, polymères, biomatériaux ou céramiques», précise le chercheur. Il souhaite maintenant utiliser la machinerie développée au laboratoire de Thoune pour un grand programme d'es- sais. «Nous souhaitons mesurer les propriétés mécaniques de matériaux entre-150°C et +1000°C, à différentes vites- ses.» Cette étude focalisée sur les micro- colonnes pourrait ouvrir la voie à une série d'importantes découvertes.